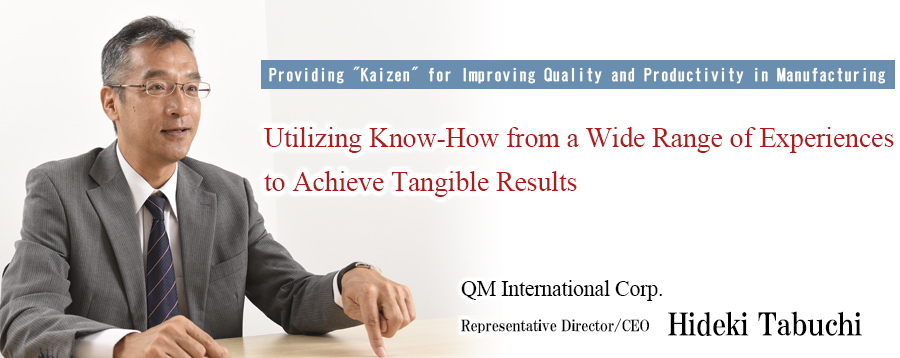
―Tell us about the history leading up to your founding of QM International.
I worked in the Quality Assurance Department handling communication equipment for a major Japanese general electronics manufacturer. For about 15 years my job was centered on improving manufacturing quality, developing test systems, and introducing and maintaining quality management systems.After that, I transferred to Germany when the company launched a German corporation that manufactured automotive parts.There, I was an accounting manager tasked with creating business plans, managing budgets, and other tasks for five years. I came back to Japan in 2009.
During my 20 years as an employee, the company went through two major corporate restructurings, one of which followed the Lehman Brothers’ bankruptcy filing.As a result, I began to believe more strongly that, even if the company didn’t collapse, I wouldn’t always be there. After all, a manager in his fifties is hardly seen as more than corporate baggage.So, naturally, I began to consider setting out on my own.
In addition to my experiences in manufacturing, accounting, and management, I was somewhat familiar with laws related to corporate activities, so I decided to become certified as a small and medium enterprise management consultant.It took me two years to become certified, but I had earned my title as an independent business owner and started my company.Based on my qualifications as a small and medium enterprise management consultant and evaluation of my actual work in the field, I had the opportunity to fulfill training orders for Japan’s "5S" methodology (which includes "sort, set in order, shine, standardize, and sustain") and Kaizen in Cambodia through the ODA program.
A proven track record is important for developmental aid provided by ODA, so following the requests for Cambodia I soon began to get orders for Mongolia, Ethiopia, Cameroon, Nigeria, Tanzania, and Bangladesh.These experiences allowed me to recognize the magnitude of overseas demand for quality and productivity improvement.
Meanwhile, Japanese Kaizen is currently a hot topic in Africa, and I find myself living there 10 months out of the year.Even though the current focus is on ODA projects, QMI is also getting ready to open up to direct orders from private companies overseas.
―What philosophies have you come to follow through your experiences?
It goes without saying that developing proposals that benefit clients and lead to actual results is key.As consultants, our job is to be of service to our clients.The criteria for our being useful is based on visible results and improved numbers.The companies QMI works with are investing their hard-earned revenue, so providing results that at least surpass that amount is imperative.
The initial corporate diagnosis is free, after which target values for improvement are determined. From there, we work toward those goals over a 6-month span with a careful eye on progress.As the results begin to be reflected in the numbers, employee motivation will naturally increase.With a strict adherence to proposals that lead to actual results, QMI is able to create a virtuous cycle that improves the quality and productivity within the company.
―Could you share with us your vision going forward?
Although QMI is a corporation, as of now I take the orders and complete the work on my own.Looking toward the future, I’d like to hire more people in order to get orders as a full-fledged company with a system capable of carrying out a wide range of tasks.To that end, it is necessary not only to expose as many potential clients as possible to Kaizen and the possibility of improving quality and productivity, but also to increase QMI’s name recognition.
I am proud that QMI is able to provide benefits without fail to clients through the introduction of our services.Through hard work every day, QMI will continue to promote Japanese Kaizen and work to increase recognition of the QMI name.
Profile
Born in April 1965, Hideki Tabuchi joined the Quality Assurance Department for communication equipment from a major Japanese general electronics manufacturer (Hitachi, Ltd.) in 1986. For 15 years, his tasks included improving manufacturing quality, automating testing, and introducing and utilizing quality management systems.Following the establishment of a local subsidiary for manufacturing automotive parts, Mr. Tabuchi transferred to Germany for five years, where he created business plans, managed budgets, and performed other tasks as an accounting manager.In 2010, Mr. Tabuchi joined a medical equipment manufacturing and sales company where he focused on rebuilding the quality management system in addition to improving quality and productivity as a dedicated technician within the medical equipment manufacturing industry.After working as a small and medium enterprise management consultant in 2013, he founded QM International Corp. in 2015 as the company’s representative director/CEO.
information