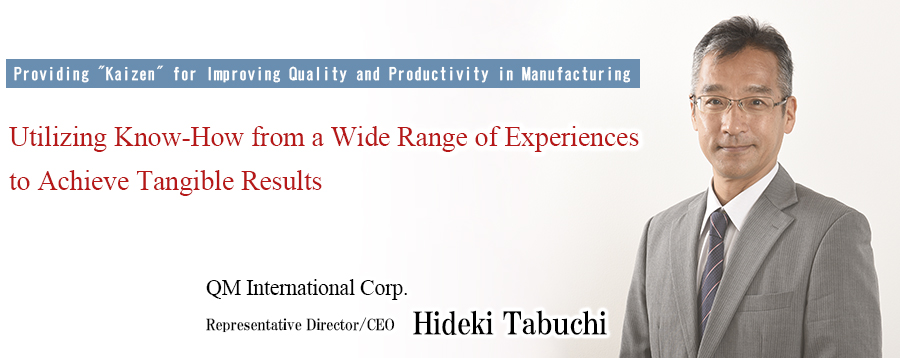
Based in Yokohama, QM International Corp (abbreviated as QMI) is active in not only Kanagawa and Tokyo but also developing countries mainly in Africa and Asia.QMI has garnered a vast wealth of experience on improving quality and productivity in the manufacturing industry, earning a recognized reputation of know-how over the years.The services offered by QMI can be labeled as "Japanese Kaizen" (continuous improvement) based on thorough on-site application of principles.We spoke with the company’s representative director, Hideki Tabuchi—a qualified small and medium enterprise management consultant with solid results in many countries and companies—about the business and services QMI offers.
― First tell us a little about the work QM International Corp. does.
QMI is a management consulting business.
Generally, QMI uses "Kaizen" methodology to provide consulting services for manufacturing industries throughout the world.Our company has focused on using Japan’s Official Development Assistance (ODA) government program to support industrial promotion in developing countries.In the future, I would like to focus our attention on offering services through direct requests from local private companies.
―What are the characteristics and strengths of the services you provide?
The "Japanese Kaizen" services QMI provides can be defined as "activities that improve quality and productivity" in the manufacturing industry.A major goal of commercial enterprises is simply producing more profit. QMI helps create profit by improving quality (which reduces raw material costs by reducing defects) and improving productivity (thus improving production capacity without increased equipment or personnel).Through this service, we investigate causes behind failures together with site managers from the client company to develop effective countermeasures with the goal of improving both quality and productivity.
Extensive practical experience in the field has given QMI its best strength—the innate ability to determine which measures will be most effective in quality and productivity improvements—which is utilized in the quest for "Japanese Kaizen".With over 20 years of experience focusing on measures against failures in manufacturing sites, QMI has developed a unique toolbox of know-how from which to borrow to improve quality.
In addition, QMI’s experience in production management at small-scale production sites has provided various skills to utilize for improving productivity, such as production planning and inventory control.I have such confidence that QMI services will deliver clear results at manufacturing sites that contracts with performance-based fees will be considered.
―What are the benefits of Kaizen services?
In terms of quality improvement, if QMI’s Kaizen services can reduce deficiencies from 5% to 2%, for example, clients can reduce costs such as raw material costs and labor costs that must be written off due to inefficiencies by more than half.Conversely, in terms of productivity improvements, if a company can produce something using eight people when usually that article takes 10 people to produce, costs will be reduced and profits will be increased accordingly.In looking at ways to enable improvements in developing countries, local consultants will be tasked with improving individual behaviors such as skill gaps and carelessness.It is often said that a lack of skills and training means such problems cannot actually be solved.This is because the background aspects, such as education and culture, are seen as unchangeable forces.But this isn’t necessarily the case. Problems can often be traced back to an inherent cause. QMI investigates that root cause to determine which points to focus on to bring about truly effective change.
The reason often cited for low productivity is " line balance problems".When it comes to the manufacturing processes behind products, there will never be a situation where all of the processes are performed at once.In about half the cases, some aspect will be simply standing by.Adjusting this aspect properly to achieve balance will make it possible to increase overall productivity.Although ideas such as these are common topics at Japanese manufacturing sites, the solutions have not yet fully caught on in developing countries.